
Incorrect Inventory - Products being out-of-stock or expired:.keeping the communication clear and straight forward will prevent confusion and mistakes, and keep your customers happy.creating a confusing customer experience through unclear instructions and industry jargon will frustrate your customers.Unclear Communication - unclear industry jargon and unclear communication:.having to contact different internal departments in order to access a service), they may lose interest along the way if your customers' experience is too segmented (e.g.making the customer journey as comfortable as possible is the recipe for success.
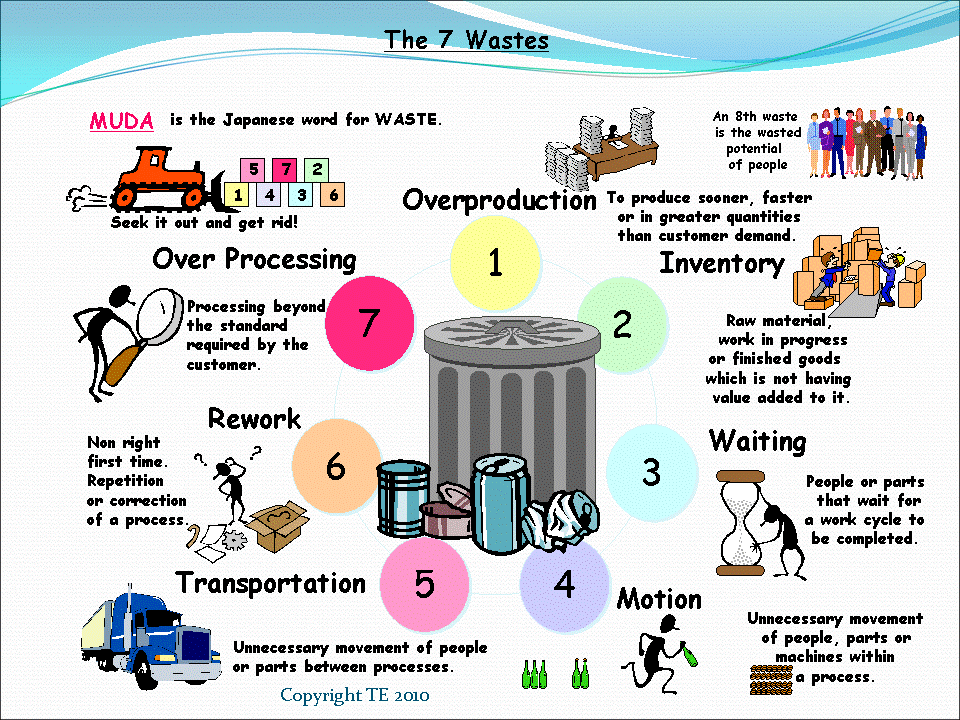

The good news is that the Seven Wastes methodology can be applied to the service industry, it just take a little thought. In fact, a surprisingly high proportion of service industry processes are wasteful without anyone noticing.
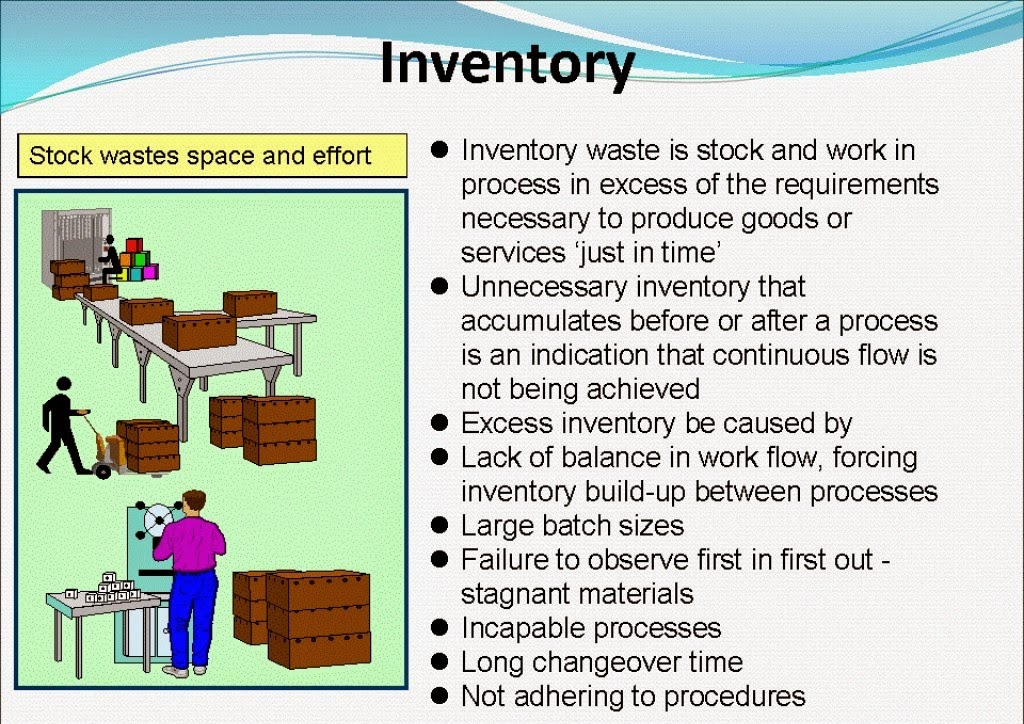
However generally the payoffs have not been nearly as dramatic for service industries applying lean principles.
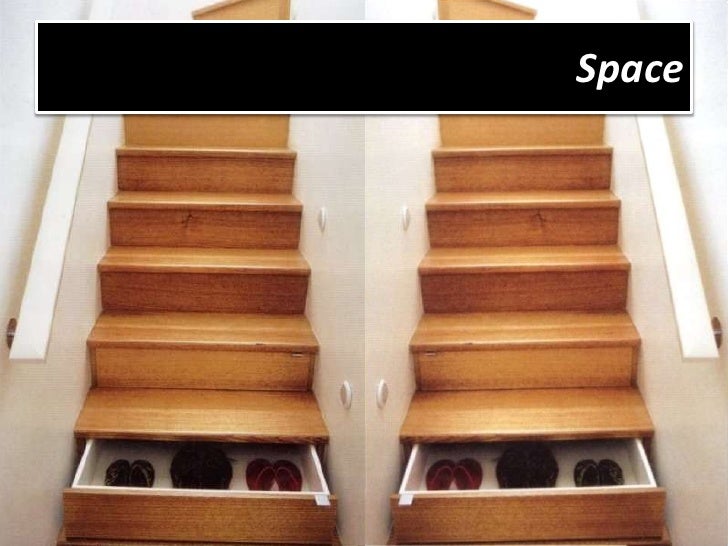
Toyota's Seven Wastes of manufacturing was a game changer for manufacturing companies in terms of maximising efficiency throughout the production process. In any industry, identifying waste can prove a challenging endeavour as you cannot always spot inefficiencies with the naked eye. You may already be aware of the 7 forms of waste in the manufacturing industry, first defined by Toyota but what about other industries where specific types of manufacturing waste aren't relevant? In this article, I explore the 7 wastes of service and how you can identify them to improve business efficiency.
